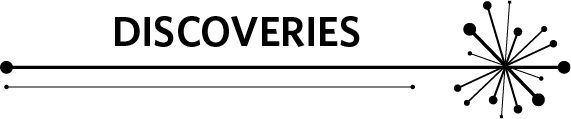
The Right Squeeze
A University of Minnesota team is using space technology to develop compression clothing for earthlings.
Space movies are tough for Brad Holschuh, who has devoted his career to inventing and developing garments to improve life not just in space but also here on Earth. So when he saw Matt Damon strolling around Mars in The Martian wearing a space suit replete with wrinkles, he wasn’t able to suspend his disbelief.
“He’d be dead,” says the assistant professor in the University of Minnesota’s Apparel Design Program, who also codirects the U’s Wearable Technology Lab with Associate Professor Lucy Dunne. “For a spacesuit to work, it has to be fully inflated.”
In fact, that inflation imperative has bedeviled space suit designers since the 1960s, when humans first traveled into space. As Holschuh explains it, a space suit needs to provide breathable air and exert enough compression—basically become a wearable balloon—to allow the body to perform the functions it does on Earth, where the weight of the atmosphere naturally places 14 pounds of pressure on every square inch of the body.
“If you were breathing a bunch of air or oxygen in space but didn’t have compression against your body, all the nitrogen in your blood would boil out of it, to the point where you’d either pass out or fail to respirate,” explains Holschuh. But these dual-function spacesuits—Holschuh calls them marshmallow suits—are so stiff and bulky, it’s almost impossible to move. That’s why the holy grail in space design has been to create a compression suit that is light and flexible. Unfortunately, gear that is tight enough to perform the needed compression function is extremely challenging to take on and off. Not to mention uncomfortable.
It’s a challenge that extends to our Earthbound compression garments, which promote healthy blood circulation and are used to treat a variety of serious health conditions, including diabetes, heart disease, lymphoedema, and burns. “People hate them,” says Holschuh. “Especially people who are elderly or in poor health—the very people who are the target market for compression therapy. They often don’t have the strength or the patience or endurance to get them on and wear them. So they stop and the treatment is ineffective.”
That’s why Holschuh and his colleagues in the Wearable Technology Lab are taking their expertise in space suit design and applying it to soft robotics—robots made of pliable materials—in order to create compression garments that initiate compression after they’re on the body. Using shape memory alloys, which are metals that remember and return to their original shape when activated, the team at the Wearable Technology Lab is designing garments that may eventually be customized according to the health needs and preferences of the person wearing them: a function that doesn’t exist in the elastic socks and inflatable compression sleeves (which need to be plugged into a power source) currently on the market.
The team recently wrapped up a two-year project with the Mayo Clinic in Rochester, Minnesota, where researchers tested a system of garments that are worn on both thighs and both calves; each can be controlled independently. They were able to replicate the health benefits of a standard compression garment, with the added benefit that it expanded or compressed when needed—and allowed the wearer to move freely because the garment didn’t need to be plugged in.
Holschuh and the team are also working with materials that can be powered by body heat rather than a battery. “Just imagine,” he says, “you put on this loose-fitting pair of pants and after a minute or two of heating up to your body’s temperature, they’ll naturally shrink-wrap down and fit you.” A user could stop compression by unzipping or unsnapping the garment. Or, says Holschuh, compression could be turned off when pressure sensors in the garment tell circuits to power down.
The Wearable Technology Lab is experimenting with other uses for these compression technologies as well, including a vest that can “hug” children with autism and sensory processing disorder, which can be switched on by a Bluetooth-enabled app. These children often benefit from the calming effects of deep-touch pressure, but they also can be easily overstimulated by direct human touch.
Rachael Granberry, a Ph.D. student in Apparel Studies, a NASA space technology research fellow, and a member of the Wearable Technology Lab, is using the lab’s shape memory alloys to make “engineered knitwear”—including a lower-body compression garment that would regulate astronauts’ cardiovascular systems after they return from space.
“The diversity of expertise in the lab makes it very innovative,” says Granberry. “I value that there are people in the lab who come from backgrounds in ergonomics, human apparel, and engineering. That spawns innovation and allows the teams to think from a more holistic perspective.”
Holschuh, who doesn’t know how to sew, also appreciates that his colleagues keep that human experience front and center. “We approach wearable technology from a clothing perspective,” he says. “To become truly ubiquitous, this technology needs to be buried in the clothing itself, in a way that doesn’t disrupt the other things that people need their clothing to do. You don’t have to think about another thing that has to be charged, that has to be synced, that has to be downloaded. . . . We’re not there yet, but that is, I think, the challenge that really needs to be solved to make this the sci-fi future, where everybody is living intertwined with technology.”
Elizabeth Foy Larsen (M.F.A. ‘02) writes for many local and national publications. She is Minnesota Alumni’s senior editor.